Optimizing your manufacturing process with an Enterprise Resource Planning (ERP) system involves several key steps and considerations. ERP systems integrate different aspects of your business, including production, inventory management, supply chain, finance, human resources, and more. Here’s a guide to help you optimize your manufacturing process using ERP:
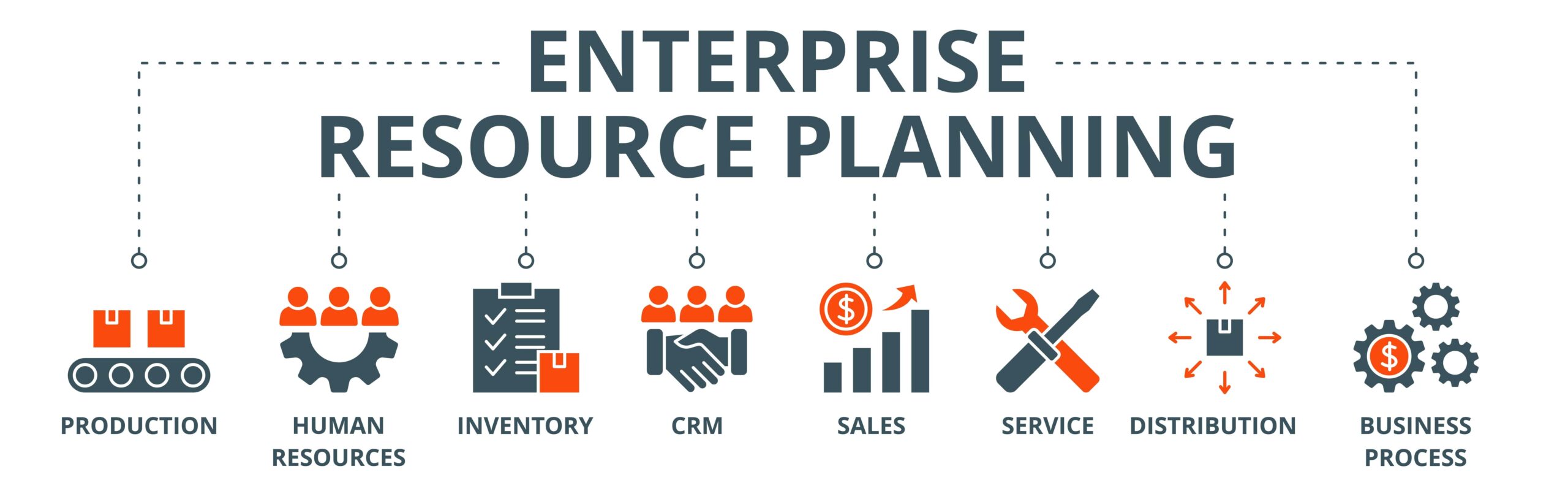
Define Goals and Objectives
Before implementing an ERP system, clearly define your manufacturing goals and objectives. Identify key performance indicators (KPIs) such as production efficiency, lead times, inventory turnover, and cost reduction targets.
Additionally, consider the specific advantages that a cloud based manufacturing ERP can offer, such as scalability, accessibility, and real-time data insights. With these goals in mind, you can tailor the implementation and configuration of your cloud-based manufacturing ERP to maximize its benefits and drive continuous improvement in your manufacturing processes.
Evaluate Current Processes
Begin by mapping out your current manufacturing processes from start to finish. Document each step involved in production, including material sourcing, production scheduling, assembly, quality control, and shipping.
Gather and analyze data related to key performance metrics such as production cycle times, equipment downtime, scrap rates, and inventory turnover. Gather feedback from stakeholders on pain points, challenges, and suggestions for improvement.
Compare your manufacturing processes against industry best practices and benchmarks. Assess supply chain disruptions, quality issues, or compliance violations. ERP systems can help mitigate risks by providing greater visibility, control, and agility across your supply chain and production processes.
Select the Right ERP System
Look for ERP systems that offer robust features tailored to manufacturing operations. Ensure the ERP system provides tools for optimizing production schedules, capacity planning, and resource allocation to meet customer demand efficiently.
Seek features for real-time inventory tracking, material requirements planning (MRP), and warehouse management to minimize stockouts, reduce carrying costs, and streamline procurement. Choose an ERP system with built-in quality management functionalities, including inspection workflows, non-conformance tracking, and root cause analysis tools to maintain product quality and compliance with standards.
Prioritize systems that offer advanced analytics and reporting capabilities for monitoring key performance metrics, analyzing trends, and identifying areas for improvement in real-time. Ensure the system can scale with your manufacturing operations, whether you’re expanding into new markets, adding product lines, or increasing production volumes.
Customization and Configuration
Work closely with the ERP consultants or vendors to tailor workflows within the system to mirror your manufacturing processes. This may involve modifying existing workflow templates or creating new ones from scratch. Each workflow should reflect the sequence of steps involved in specific tasks or processes, such as order processing, production scheduling, or quality assurance.
Customize data fields and attributes within the ERP system to capture relevant information specific to your manufacturing operations. This could include product specifications, batch numbers, production dates, or quality control parameters. By customizing data fields, you can ensure that the ERP system accurately records and tracks the information essential for your business processes.
Streamline Production Planning and Scheduling
ERP systems facilitate seamless coordination between production planning, inventory management, procurement, and other relevant areas, ensuring that decisions are made based on accurate, real-time information.
Demand forecasting is a fundamental aspect of production planning. The forecasts serve as the basis for production schedules, enabling businesses to align their manufacturing activities with anticipated customer needs.
ERP systems help businesses assess their production capacity and identify potential bottlenecks or constraints. By considering factors such as equipment capacity, labor availability, and lead times, organizations can develop realistic production schedules that minimize idle time and optimize resource utilization.
Inventory Management
Implementing ERP modules for inventory management enables businesses to track inventory in real-time, optimizing control over raw materials, work-in-progress, and finished goods. Features like reorder points, safety stock levels and automatic replenishment prevent stockouts and minimize carrying costs. ERP systems integrate data from procurement, production, and sales, providing up-to-date visibility across the supply chain.
Automation streamlines processes, reducing lead times and improving inventory turnover. Advanced tools like demand forecasting and inventory optimization algorithms enhance decision-making by predicting future demand accurately. Comprehensive reporting and analytics allow businesses to monitor key performance indicators.
Quality Control and Compliance
Inspection checklists, digitized within the ERP, automate inspections, reduce errors, and maintain detailed records for auditing. Non-conformance tracking identifies deviations from standards, enabling root cause analysis and timely corrective actions.
ERP-triggered workflows streamline corrective actions, minimizing disruptions to production and customer satisfaction. Compliance management features centralize regulatory requirements and documentation, facilitating audits and demonstrating adherence to regulations.
Supply Chain Management
Through the ERP system, businesses can monitor supplier performance, manage vendor relationships, and optimize logistics to reduce lead times and costs. Real-time access to data allows for objective assessment of supplier performance, facilitating better collaboration and risk mitigation.
Furthermore, effective management of vendor relationships fosters trust and promotes innovation throughout the supply chain. By leveraging advanced features such as demand forecasting and inventory optimization algorithms, businesses can further enhance efficiency and minimize stockouts.
Conclusion
Now, you’re ready to optimize your manufacturing process with ERP. Just ensure that you regularly review performance metrics, solicit feedback from employees, and identify opportunities for further optimization. Provide training and support to ensure employees are proficient in using the ERP system effectively. Talk to an expert on ERP for tailored assessment and solution offers.